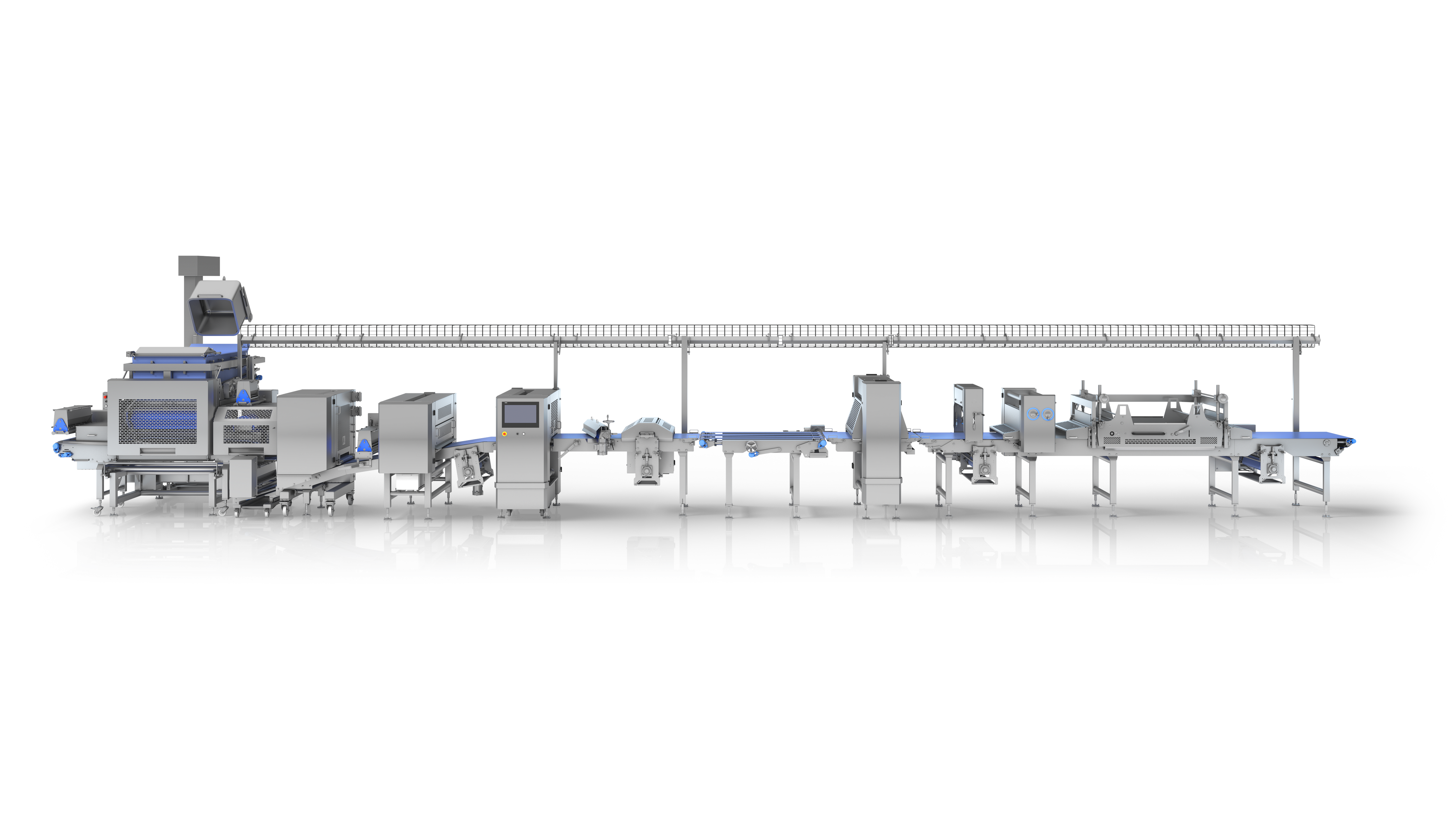
What happens when FRITSCH listens to its customers in large and industrial-sized baking enterprises?
Exactly what their production and shift managers have wanted: an overview of the most important performance data of the equipment in as close to real time as possible. Even including any downtimes caused by minor malfunctions as well as the maintenance status of the line.
Smart Production Insights (SPI) by FRITSCH now offer all that and more. “We always wanted to give our customers a live insight into their production processes and thus create the highest degree of transparency,” says Wolfgang Stegmaier, Project Manager for Digital Development at FRITSCH. Now, with the continuous capture of data and visualisation of key performance indicators in real-time, producers will be able to achieve targeted improvements in overall equipment effectiveness.
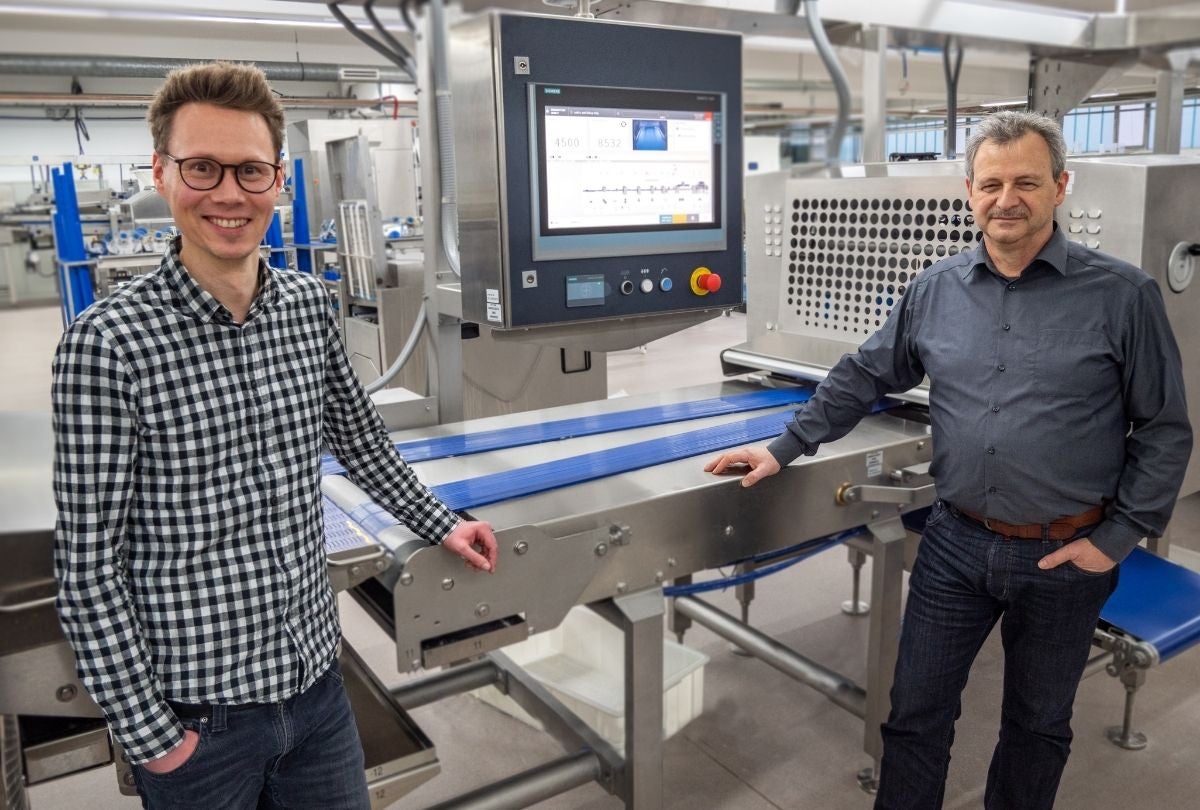
Lots of little problems can add up to one big one. Knowing this, the digitalization team led by Wolfgang Stegmaier and colleague data analyst Stefan Eydel at FRITSCH decided it was time there was a solution that addressed exactly this phenomenon. The technicians, software specialists and data experts therefore developed Smart Production Insights, which takes a rather unusual approach: the technology records and graphically displays even minor faults that occur from time to time during production. Until now, production or shift managers had no way of responding to these short-lived faults because they were never even detected.
„Often, they are only fleeting problems that interrupt production for maybe two to five minutes at most. But if that occurs multiple times during the whole shift, then it all adds up to unplanned production downtime in the end“, Stefan Eydel says, outlining the problem.
Customers can now inspect the data from SPI to find out exactly what causes these faults, and take the right steps to prevent further related equipment downtimes. "What I especially like about this project is that it’s a completely new product, which we’re all developing and upgrading together as a collective collaboration", Eydel explains.
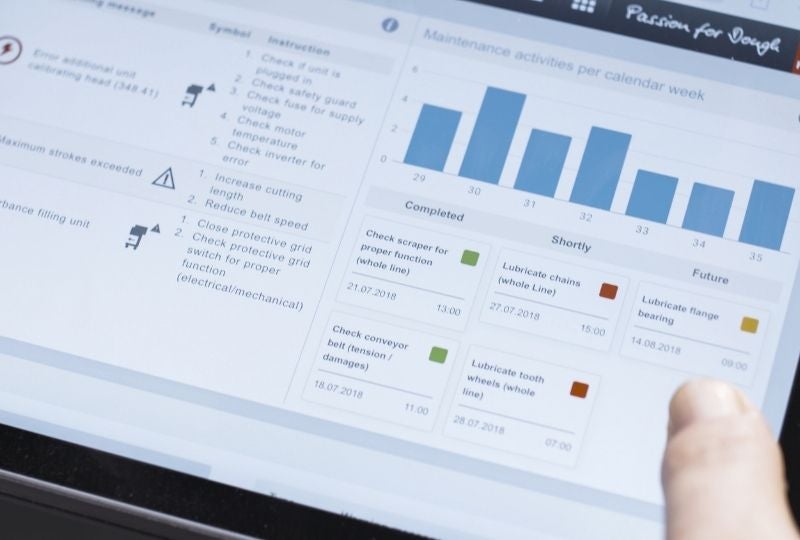
Well prepared data paves the way for targeted improvements
The Smart Production Insights are not only available as an additional service for new lines, but can also be retrofitted to many existing lines as well. It comes with a dashboard that shows the total line efficiency, equipment availability, and performance in terms of the number and quality of pieces produced.
“Also, given a simple tabular overview, the production or shift managers can immediately recognise how the equipment has been operating over the last 24 hours,” says Wolfgang Stegmaier. The electrician and master of electrical design, who has been delving deeply into digitalisation of production lines since 2017, has a strong technical understanding of FRITSCH machines.
The smooth-running team is making real improvements to the digital services and thus bringing the benefits of the digital revolution to the customers. “Producers can not only compare the results between different shifts, but also monitor their production runs live,” Stegmaier reports. They can use these real-world production figures to create more precise plans and thus more accurate schedules for delivering to their customers. Equipment effectiveness can be improved further still by targeted analysis and troubleshooting, combined with a clear overview of upcoming maintenance times.
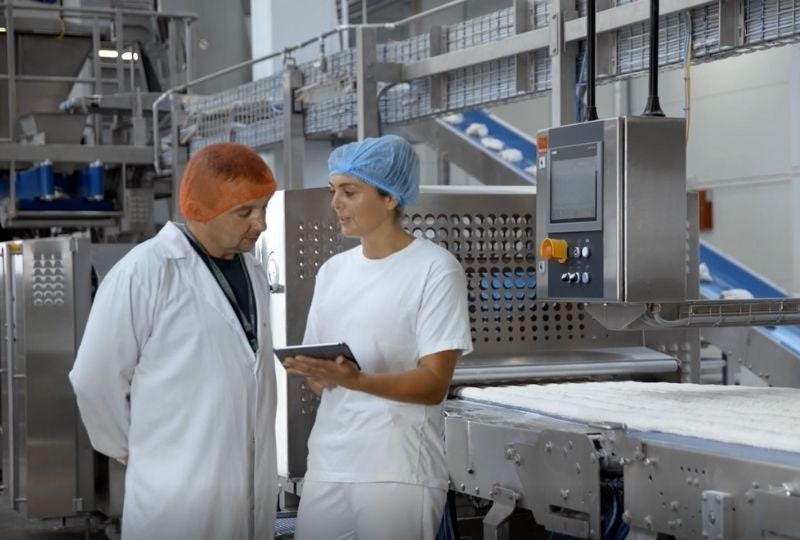
Started at FRITSCH, continued with MULTIVAC
The first steps towards digitalisation were already taken at FRITSCH in 2018, with the definition of structures for data collection from the controllers and the development of a dashboard. The system was first revealed to customers at iba 2018. “We even received the 2018 iba Award already for this initial development. That was of course a wonderful success for our newly composed team,” Stegmaier recalls.
As the digitalisation wave rolls on, Wolfgang Stegmaier, Stefan Eydel and the entire team at FRITSCH will continue working on more digital products. “An important source of information for us is of course the reviews of our customers, who day after day produce millions of rolls, pretzels, croissants, breads and fine pastries on our lines,” says Stefan Eydel. Just like in their collaboration on developing SPI, the FRITSCH team can continue to rely on the proven expertise of the MULTIVAC colleagues as they work towards the same goal: to continually improve the services for the customers so that, thanks to insights gained from data analysis, unplanned equipment downtimes soon become a thing of the past.
"After the acquisition of FRITSCH, the digitalisation specialists of MULTIVAC joined to continue developing the system, up to the point where it is now a mature product available to the customers under the name of Smart Production Insights,” the project manager explains.
“We even received the 2018 iba Award already for this initial development. That was of course a wonderful success for our newly composed team.“
Wolfgang Stegmaier, Project Manager for Digital Development
The FRITSCH Smart Production Insights
Read more stories
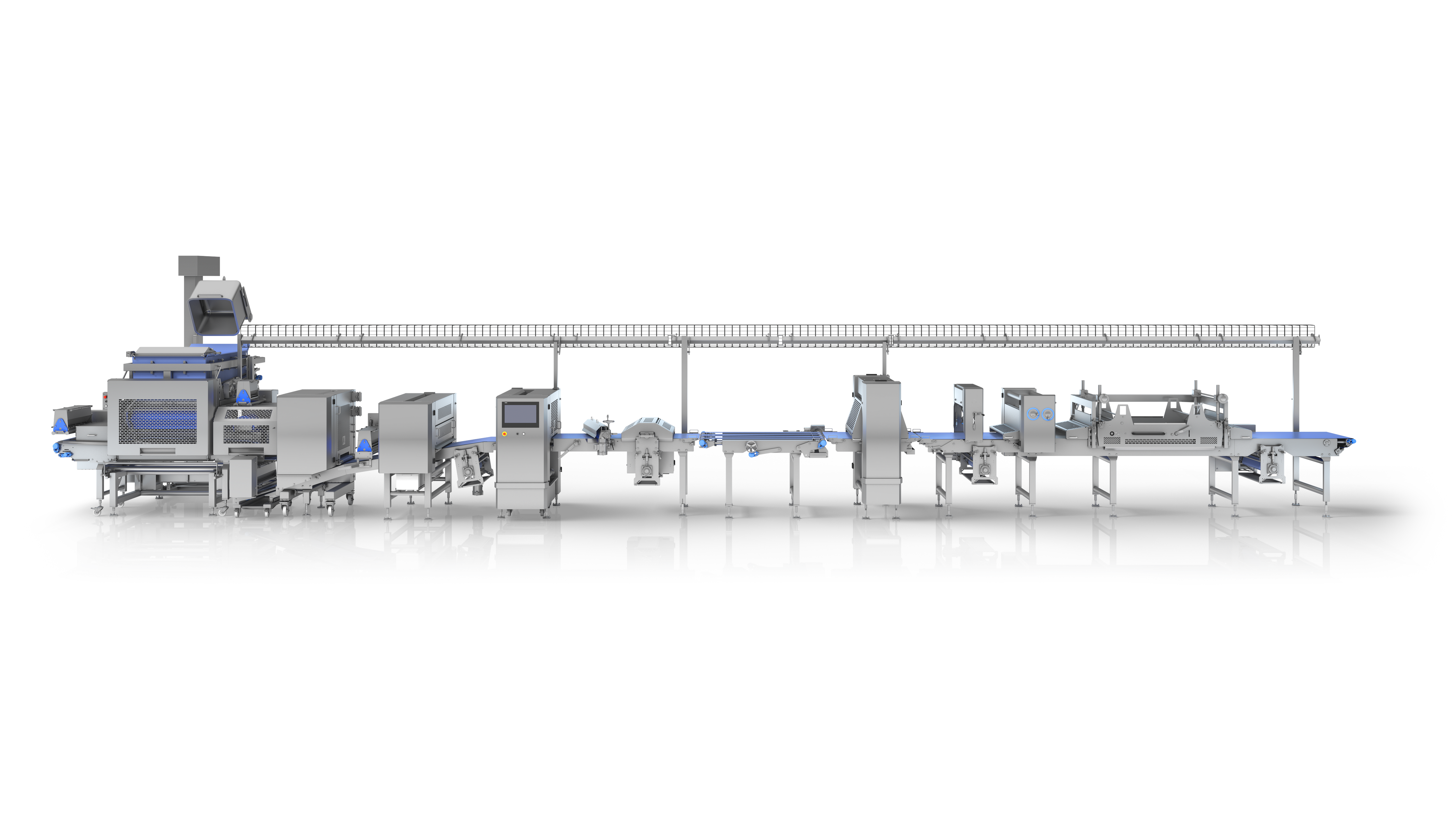
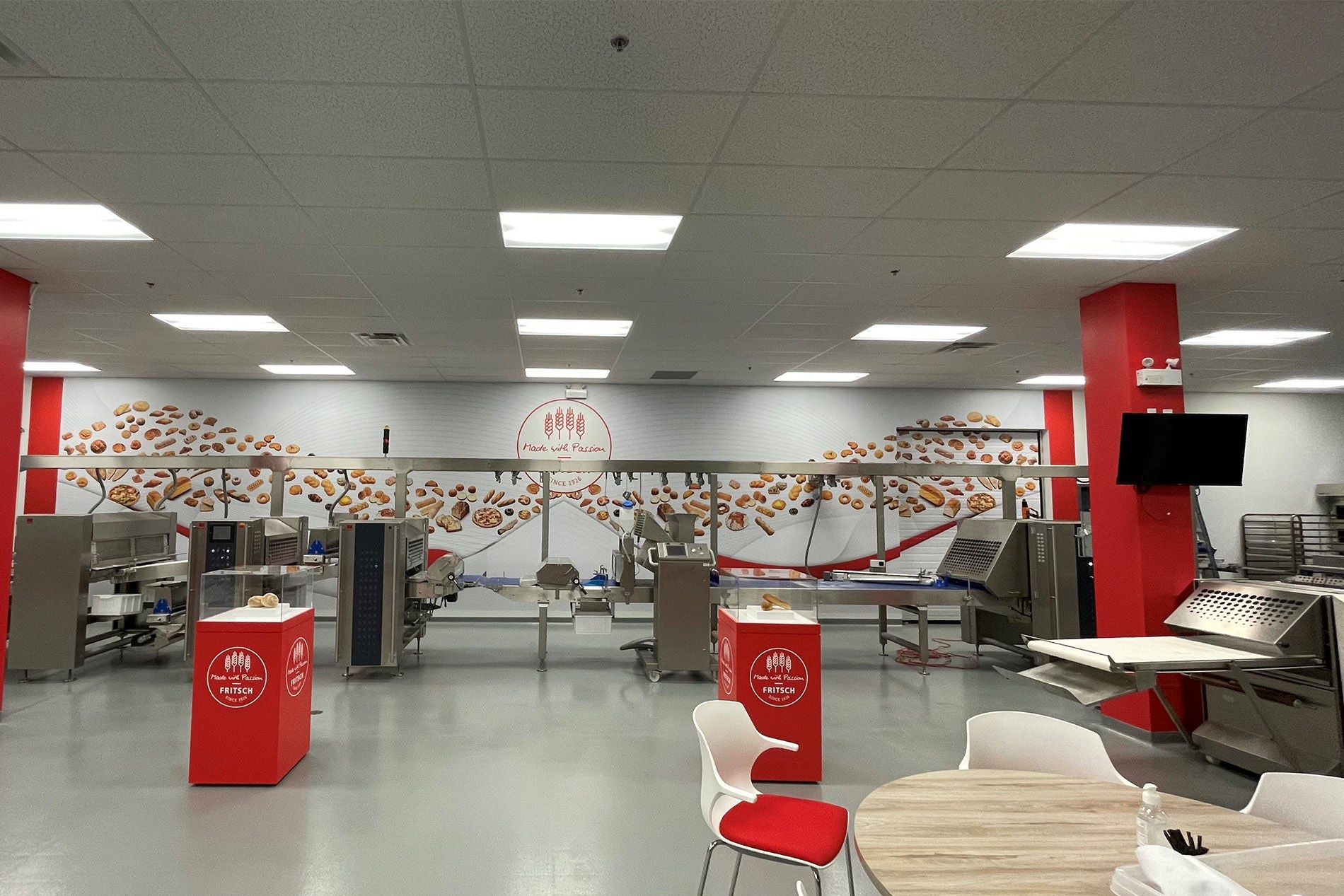
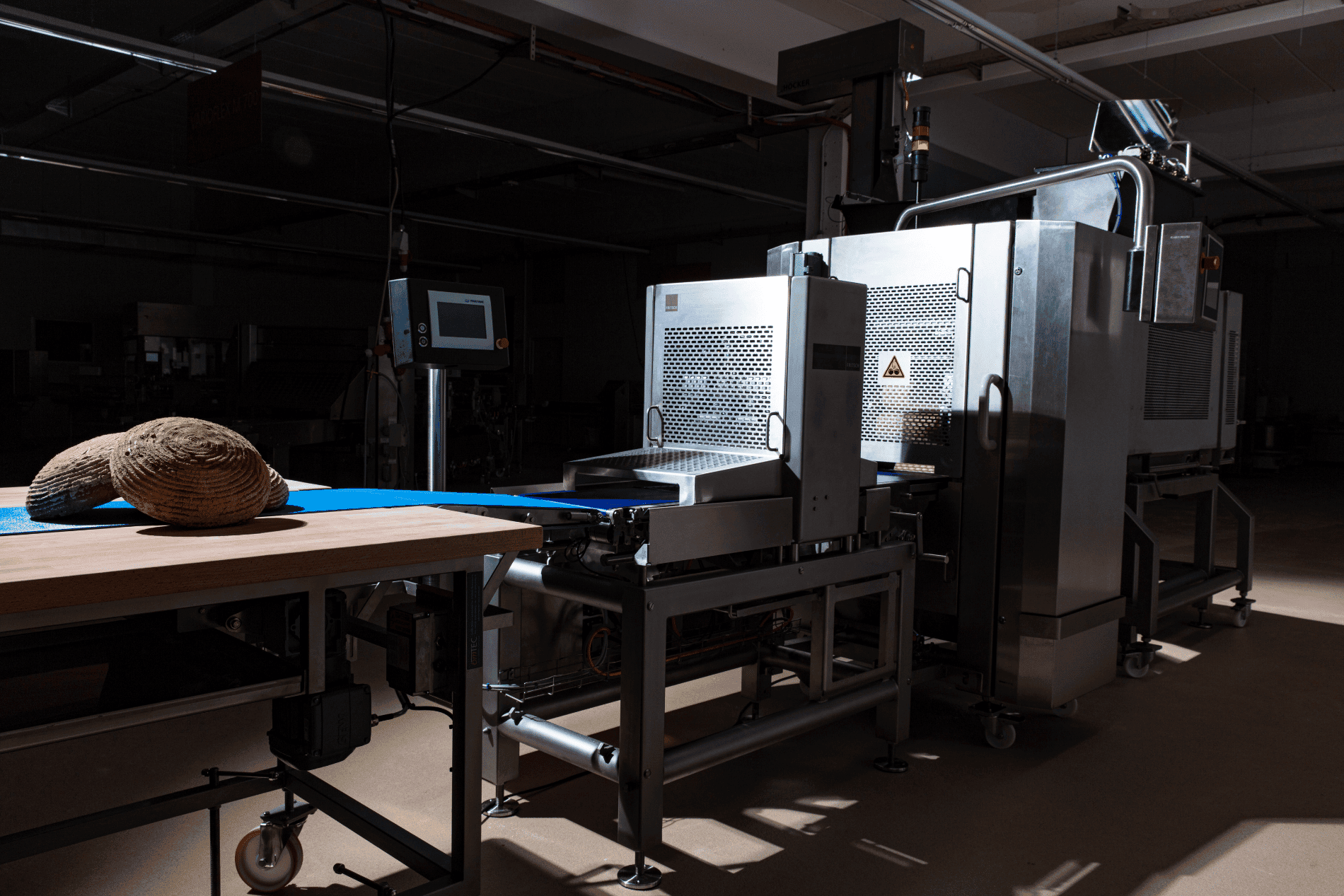
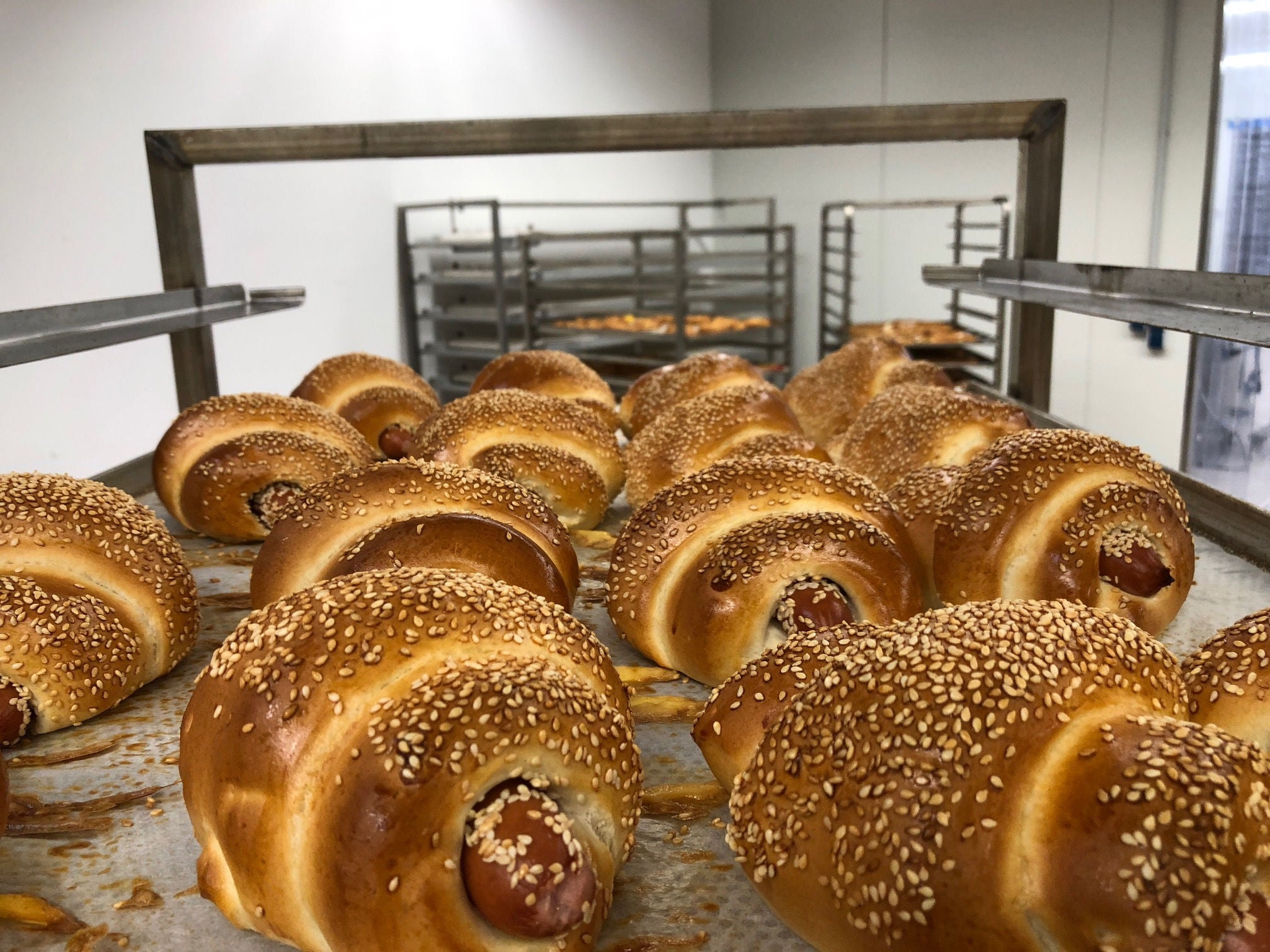
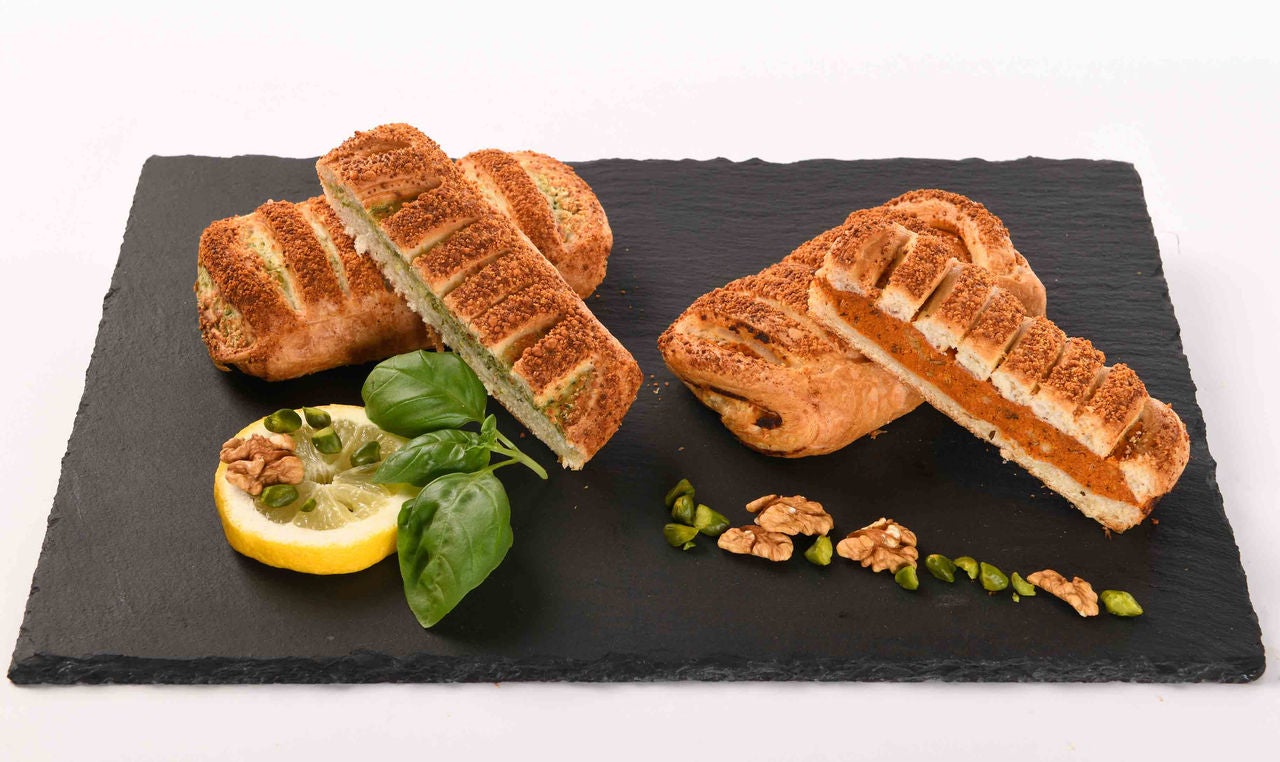

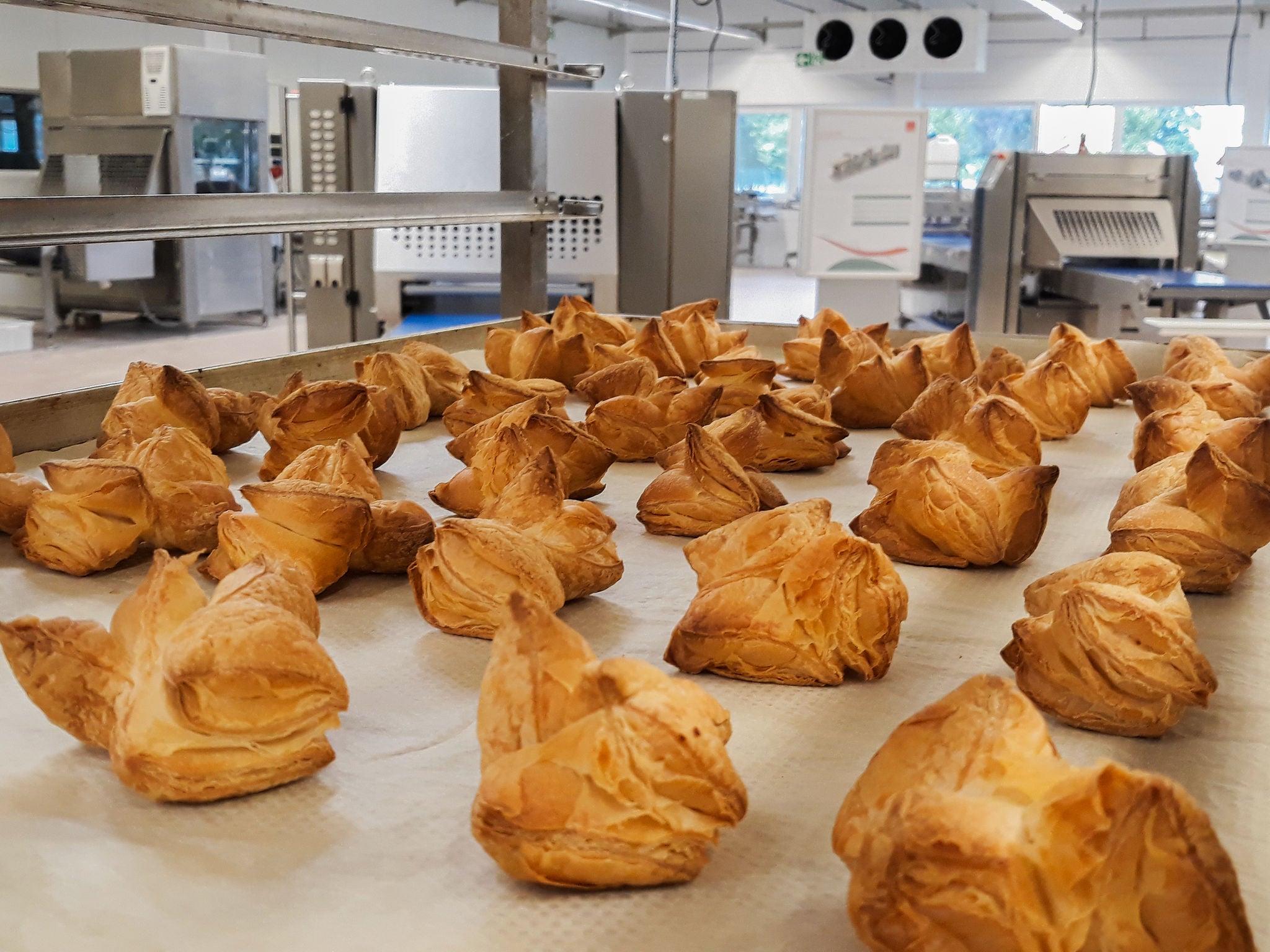