This is what FRITSCH Smart Services can do for you
Availability and efficiency
Thanks to its groundbreaking digital solutions, FRITSCH offers a wide range of tools to increase machine availability, performance, quality, and efficiency. In addition, transparent processes and real-time data contribute to the overall and cost-effectiveness of machines and lines.
Connected and convenient
With digital products and services from FRITSCH, we offer you innovative solutions for monitoring, controlling and optimizing production - also available across locations from anywhere in the world and accessible via any device, simply via the cloud. Uncomplicated, immediately usable and live. For new systems and for retrofitting existing machines.
Easy to set up and constantly evolving
The use of FRITSCH Smart Services does not require a significant start-up investment. The well-established standard range of digital solutions is constantly being improved and developed further - with the focus always on customer needs.
- Smart Production Insights
- Watchdog
Smart Production Insights
This Smart Service gives production and shift managers a clear dashboard with real-time insight into the line's key performance data.
Even downtimes due to minor interruptions are clearly recorded so that measures to prevent them can be initiated quickly and easily. By continuously recording data and visualising key performance indicators in real time, significant improvements in overall line efficiency can be achieved.
- Overall Equipment Effectiveness
- System status over the last 24 hours
- Production overview (target vs. actual)
- Shift Comparison
- Warnings and maintenance
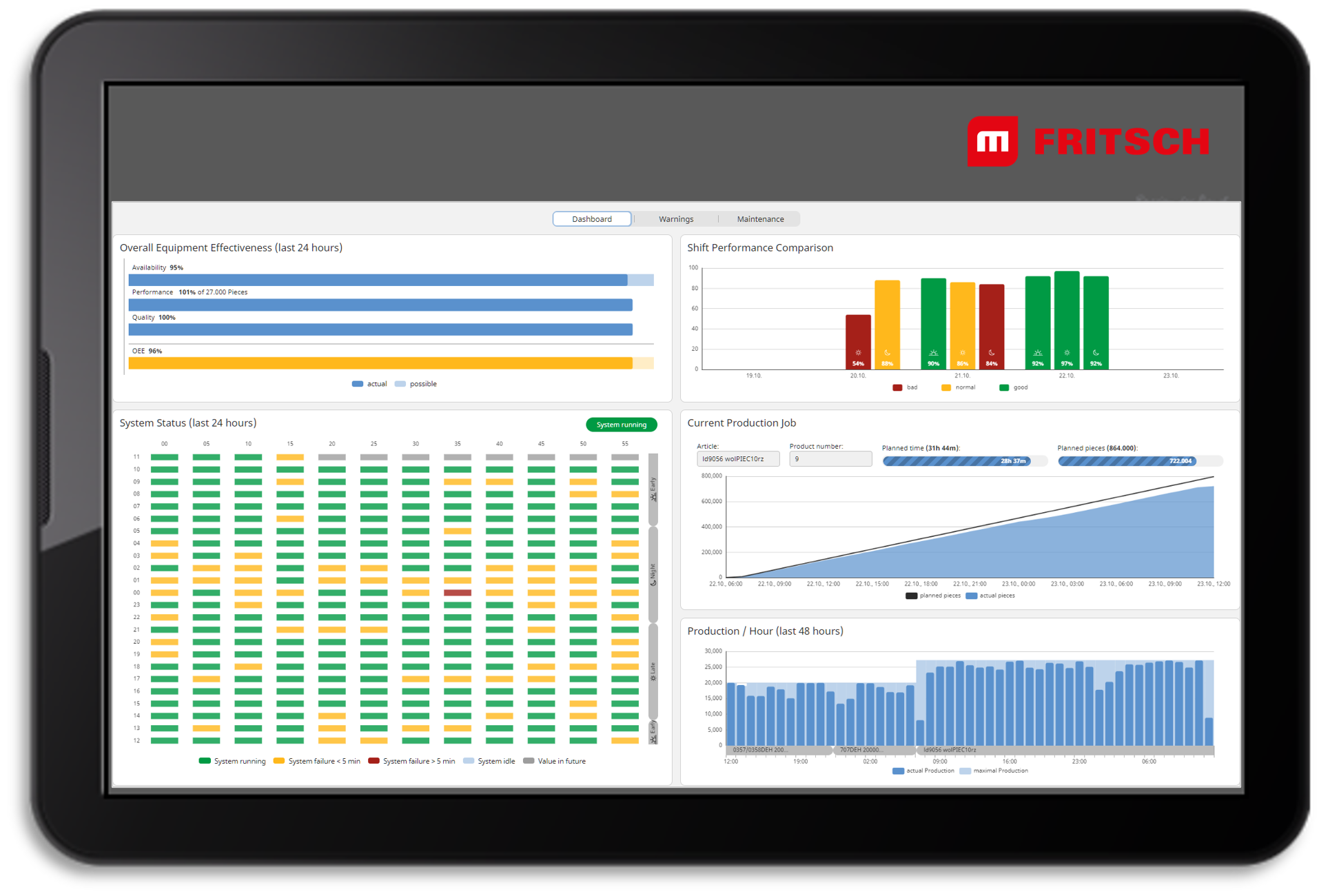
Watchdog
The Watchdog continuously measures and analyses the motor current and temperature of each drive on the line. Watchdog calculates a reference value that is used to show the condition of the drive and monitors if it lies within a pre-defined range. As soon as this reference value crosses the lower or upper threshold, a warning is issued to a specified group of people.
Thus, they are able to react accordingly before the drive unit gets damaged or even breaks down completely. With this system of predictive maintenance, unplanned downtimes can be reduced or even avoided completely.
As an example, in case of a motor nearing or exceeding the threshold, spare parts that customers usually do not keep in stock can be ordered in good time and built in during scheduled maintenance and repair jobs.
The Watchdog
- measures and analyses data from all drives of the line
- identifies components that are potentially at risk of failure
- informs the responsible group of people via email about a reference value outside of the threshold
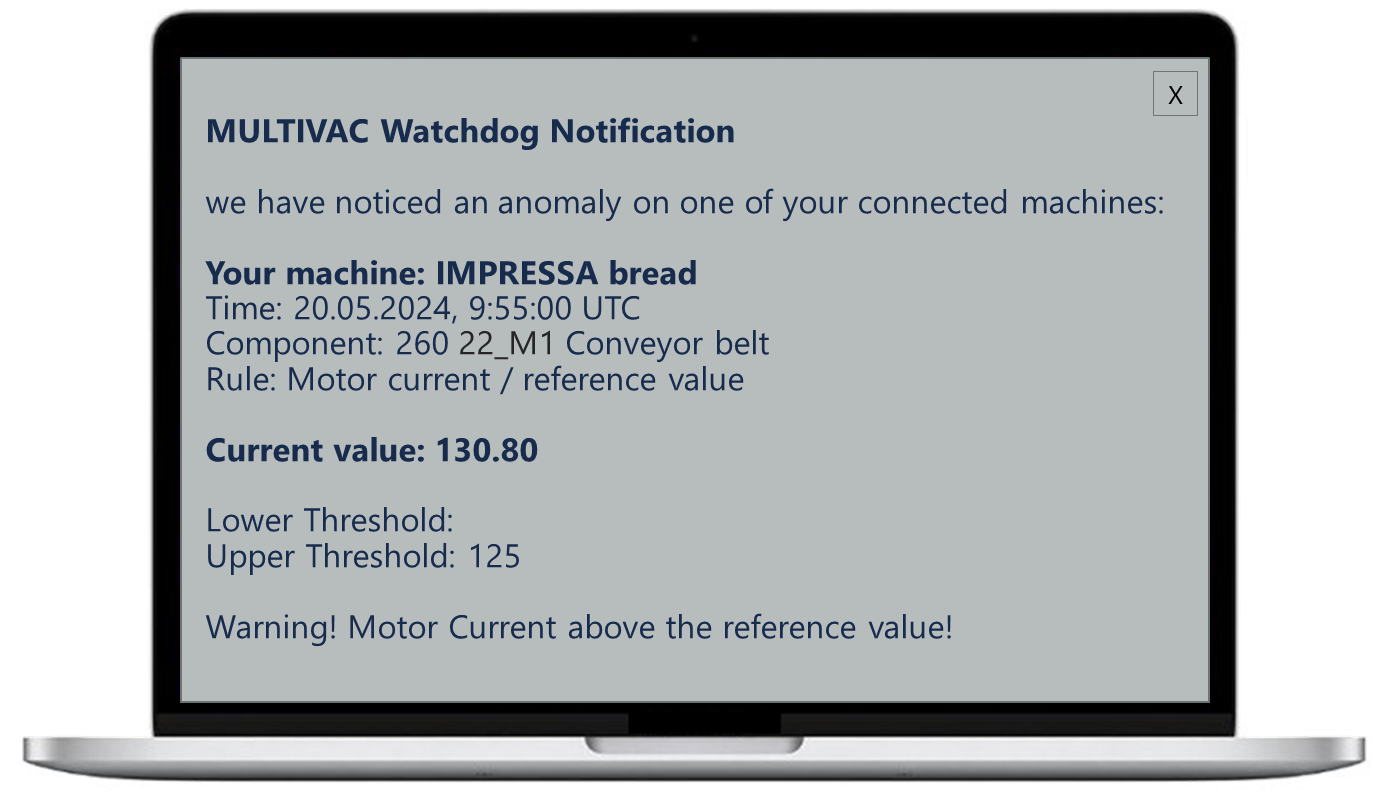