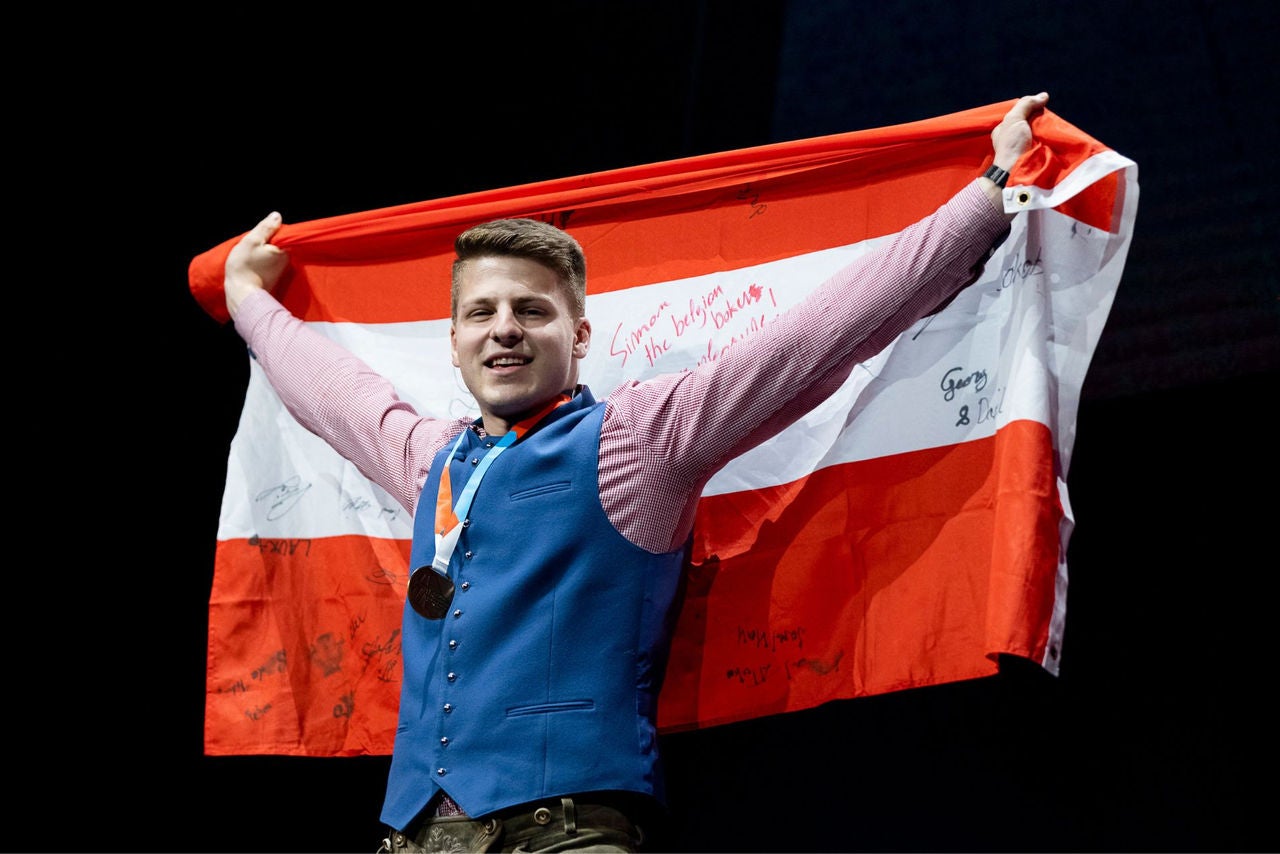
In Marki, a small town on the outskirts of Poland’s capital Warsaw, the bakery company Inter Europol is writing an amazing success story thanks in part to its production lines from FRITSCH. Rüdiger Stollmeier, a project manager at the company for 13 years, has played a significant role in this by continually using innovations to increase the efficiency of the lines. Some months ago, he achieved yet another boost by installing FRITSCH’s digital solution Smart Production Insights on two IMPRESSA bread lines at the company’s second location in Malopole.
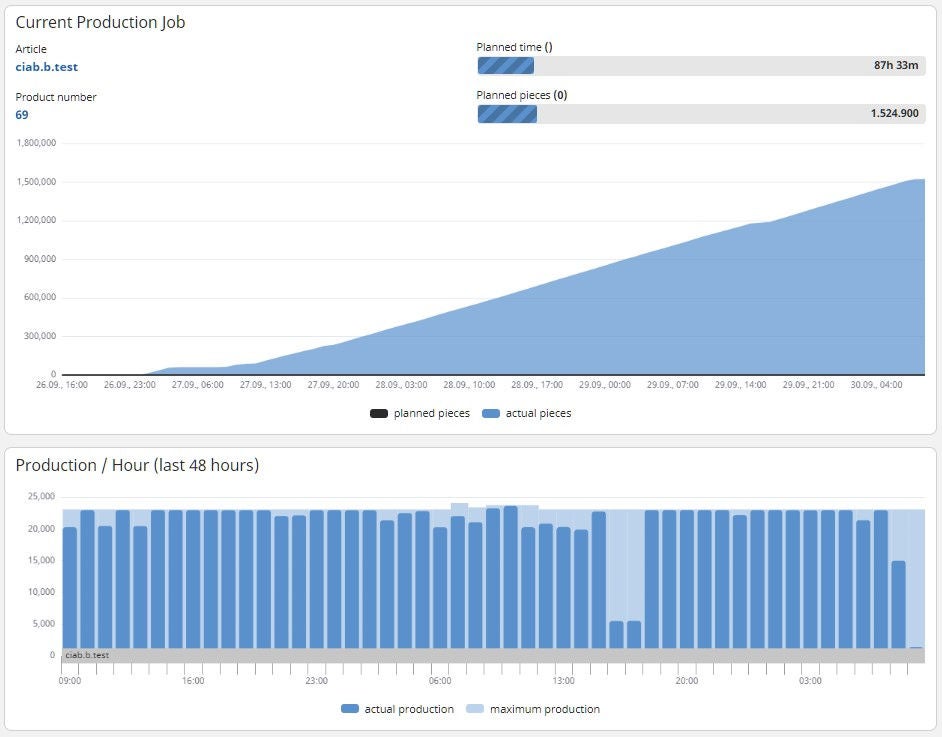
FRITSCH has been offering this digital solution for certain lines since autumn last year. Over an internet connection and the cloud, Smart Production Insights (SPI) provides a highly detailed, real-time overview of the most important performance data of production lines like the IMPRESSA bread. The information displayed on the dashboard ranges from time lost due to minor malfunctions to detailed error messages and the exact maintenance status of individual components on the line.
This live overview of production offers maximum transparency for production and shift managers.
All key figures at a glance
At Inter Europol, Smart Production Insights is currently used by the technicians who manage the two IMPRESSA bread lines. Rüdiger Stollmeier is most impressed by the dashboard display. “On it, I can find all the important production information at a glance,” Stollmeier explains.
A bar graph on the graphical display, for example, clearly shows the overall efficiency of the line. Each bar shows percentage figures for the past eight-hour shifts over the last several days.
"This allows us to analyse and compare the performance of different shifts. From that, we know where we can make improvements.“
Rüdiger Stollmeier, Project Manager at Inter Europol
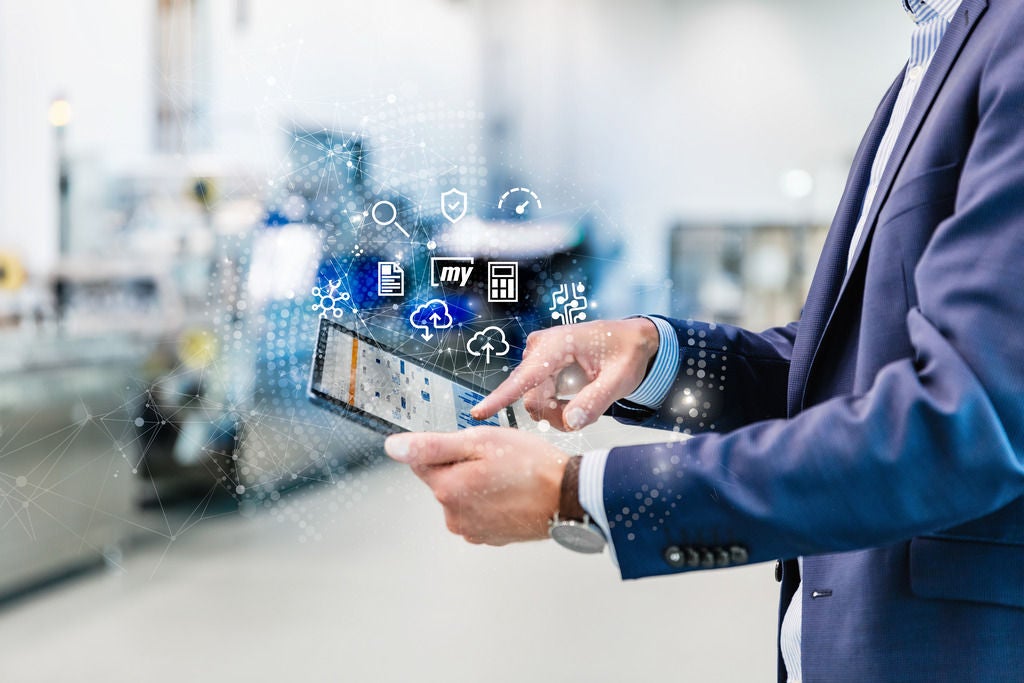
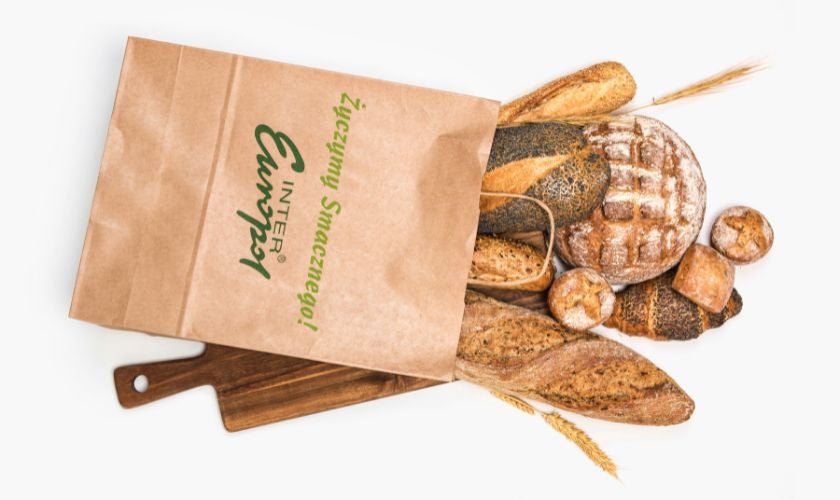
Another overview that Smart Production Insights provides is a simple table with a traffic light system indicating the line’s performance over the last 24 hours. This is shown in five-minute intervals: a green area indicates smooth production, a yellow area indicates minor malfunctions, and a red area indicates that the line was at a standstill for some time within that five-minute interval. Additonally, the colour blue is used for indicating cleaning and maintenance work.
Technicians are of course mostly concerned about yellow and red fields. Clicking on each field brings up the corresponding error messages. “This tool makes troubleshooting easier and enormously speeds up finding and fixing faults,” says Stollmeier. “While I can’t precisely quantify the cost savings this achieves, it is definitely significant.”
Being in regular communication with its customers, FRITSCH in turn uses the knowledge gained from these precise fault analyses for making continuous improvements to its lines. Of course, Smart Production Insights doesn’t just display faults that have already occurred, but also generates warnings when individual components are running hot or threatening to fail. This enables shift supervisors and technicians to react in time and to avoid potential downtimes.
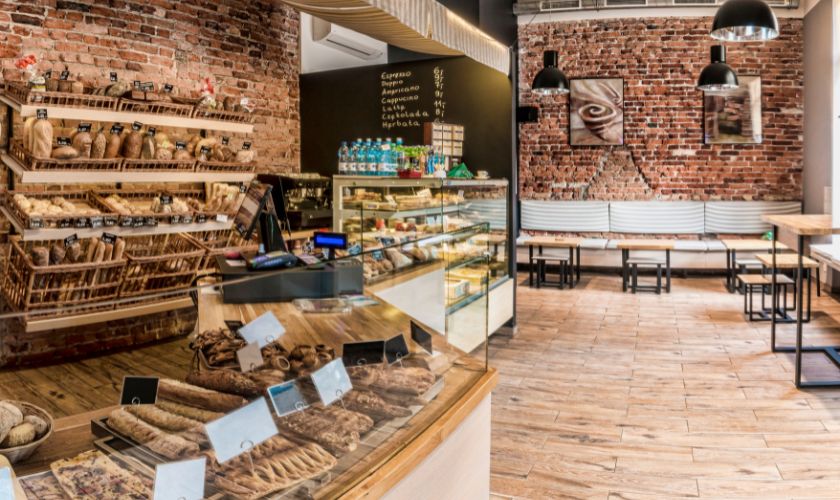
“We once had a warning showing a motor was outside of the specified temperature range, and a targeted inspection then revealed that a ball bearing was slightly defective. As a result, our technicians were able to replace the bearing and prevent even more downtime,” Stollmeier says, describing a case, where targeted repair was triggered by real-time data.
Better prepared for maintenance intervals
Naturally, not every warning means the line has to be shut down immediately. Often, it is safe to continue operating until the next maintenance interval before fixing the indicated problems. If this requires certain spare parts, the responsible department can check whether they are in stock or whether they have to be ordered.
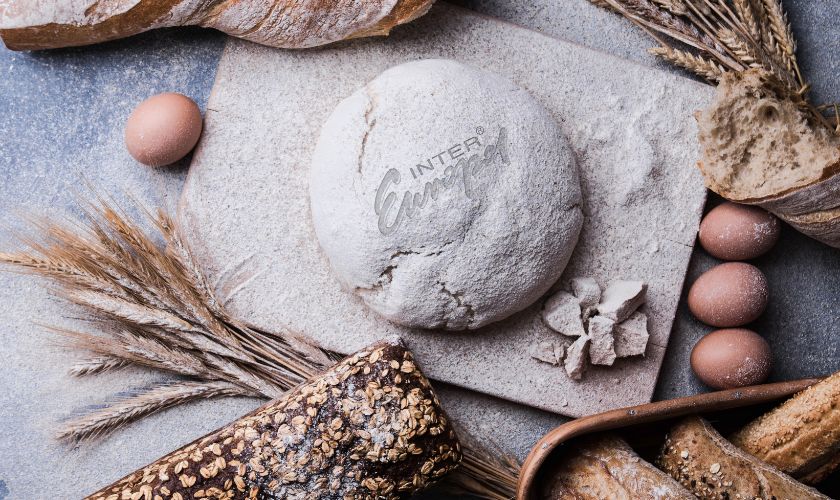
When it comes to maintenance, Smart Production Insights again provides a precise overview of what, where and when scheduled work is due. FRITSCH has precisely defined maintenance tasks and intervals in a user manual, based primarily on the running time of the line. “When I click ‘Maintenance’ on the screen, I immediately see what tasks need to be carried out in the near future and what maintenance work was last done,” Stollmeier explains. “This allows our technicians to prepare better and get the maintenance done faster. That, in turn, reduces downtimes and improves the overall efficiency of the line.”
The many advantages of Smart Production Insights are felt not only by technicians, but also in production management. Should malfunctions or maintenance ever lead to long, unexpected downtimes, this can be taken into account in purchasing. “On large lines like these, which process several tonnes of flour per hour during production, Purchasing can cancel flour orders if necessary,” says Stollmeier. Given the many advantages, Inter Europol is planning to retrofit as many of its other lines as possible with Smart Production Insights in the near future.
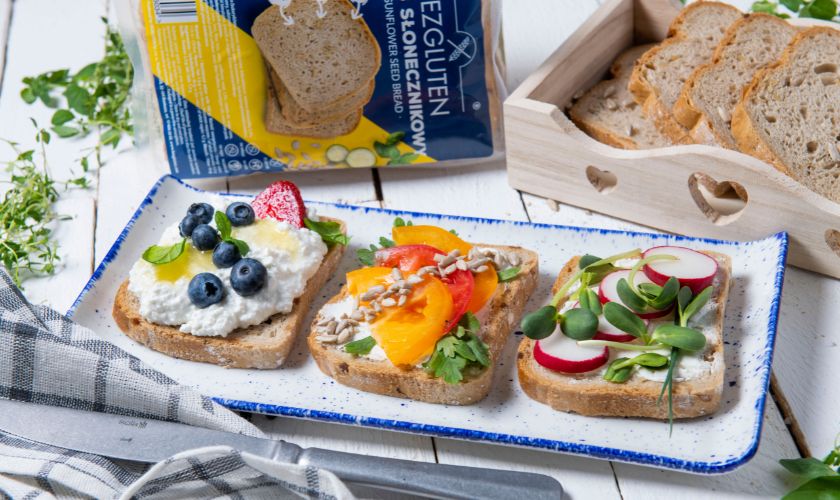
Further references
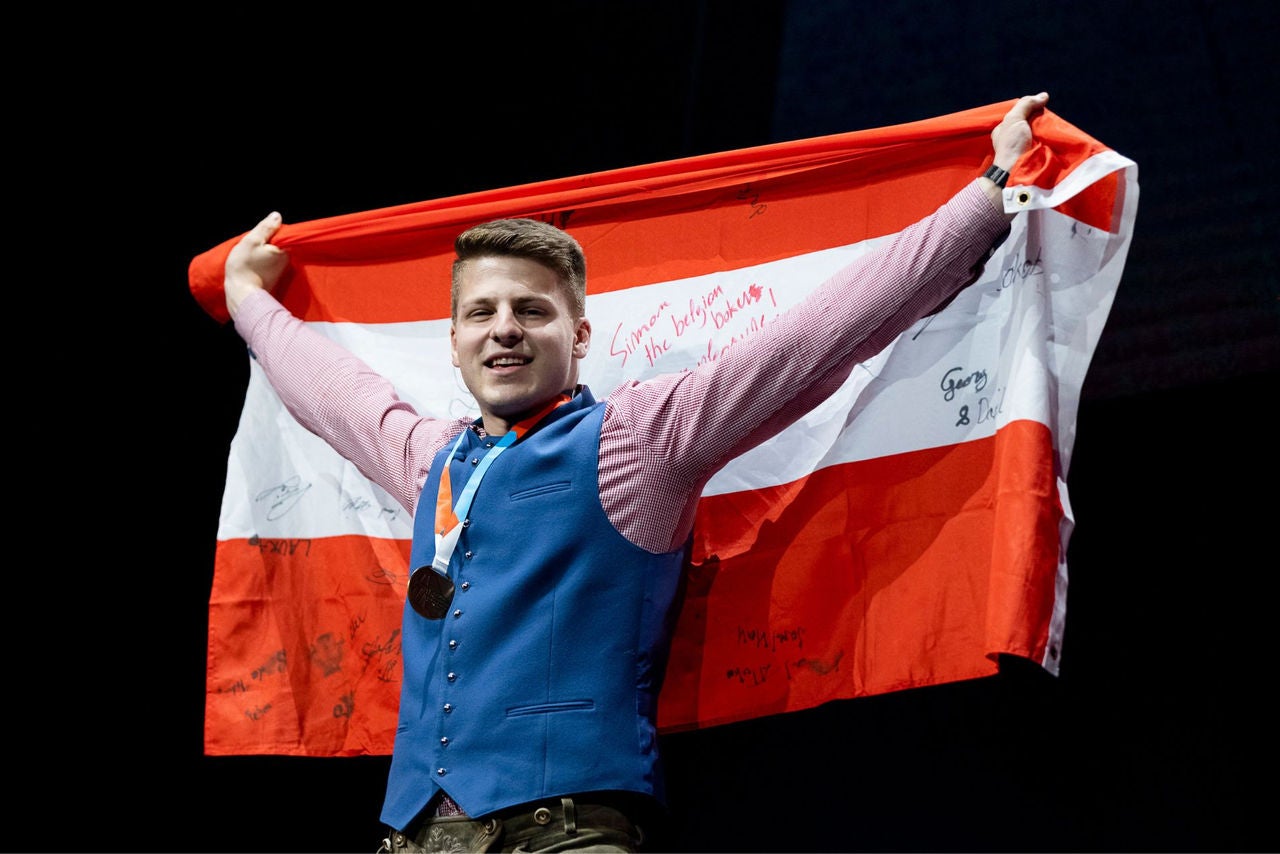
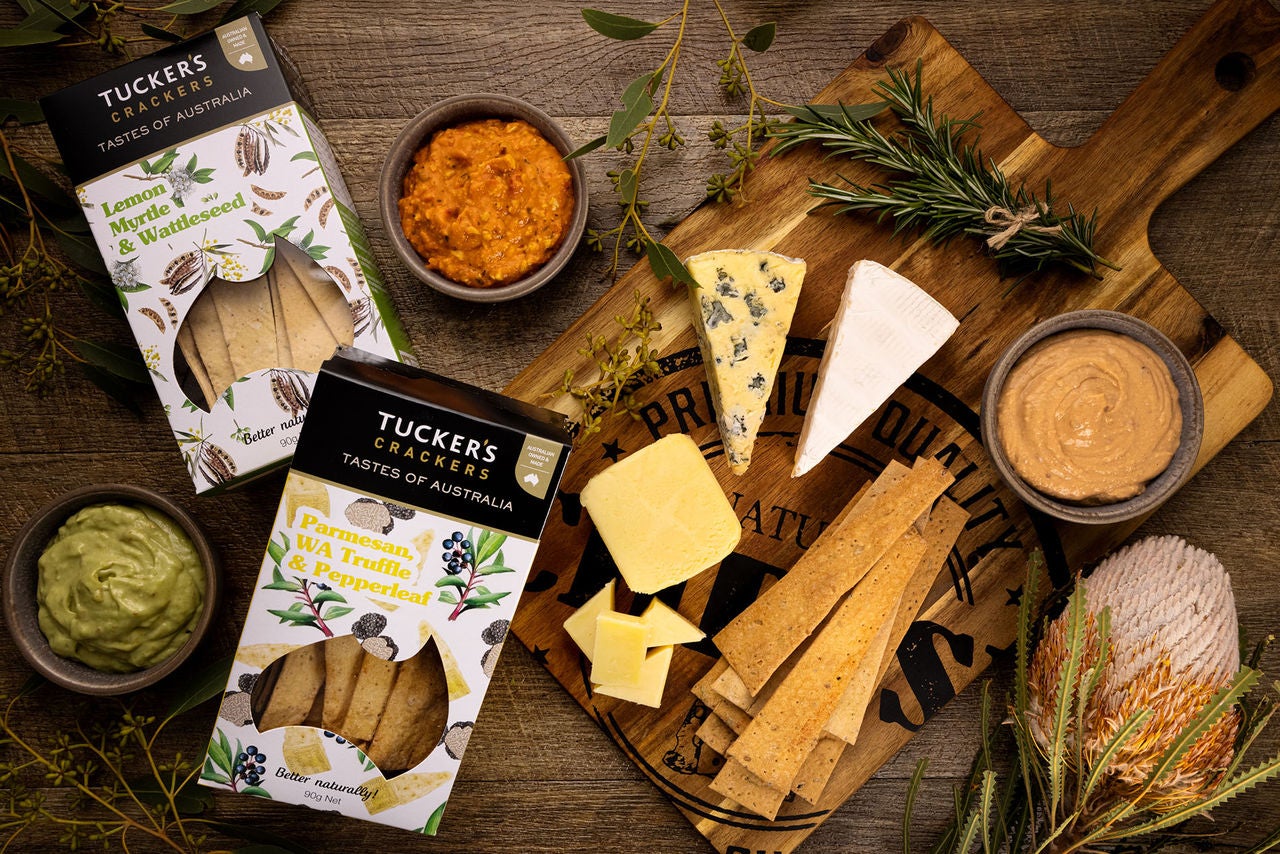
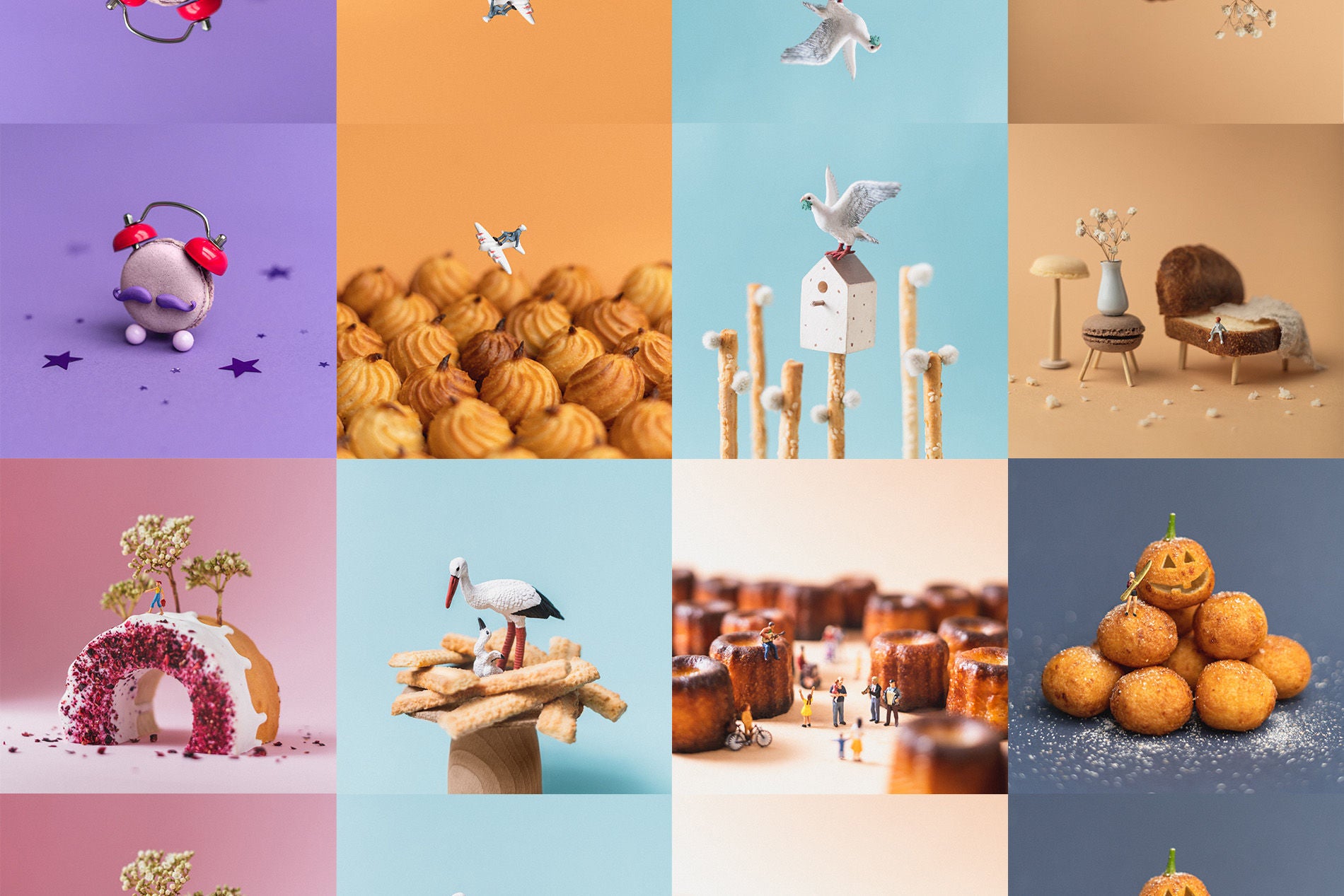
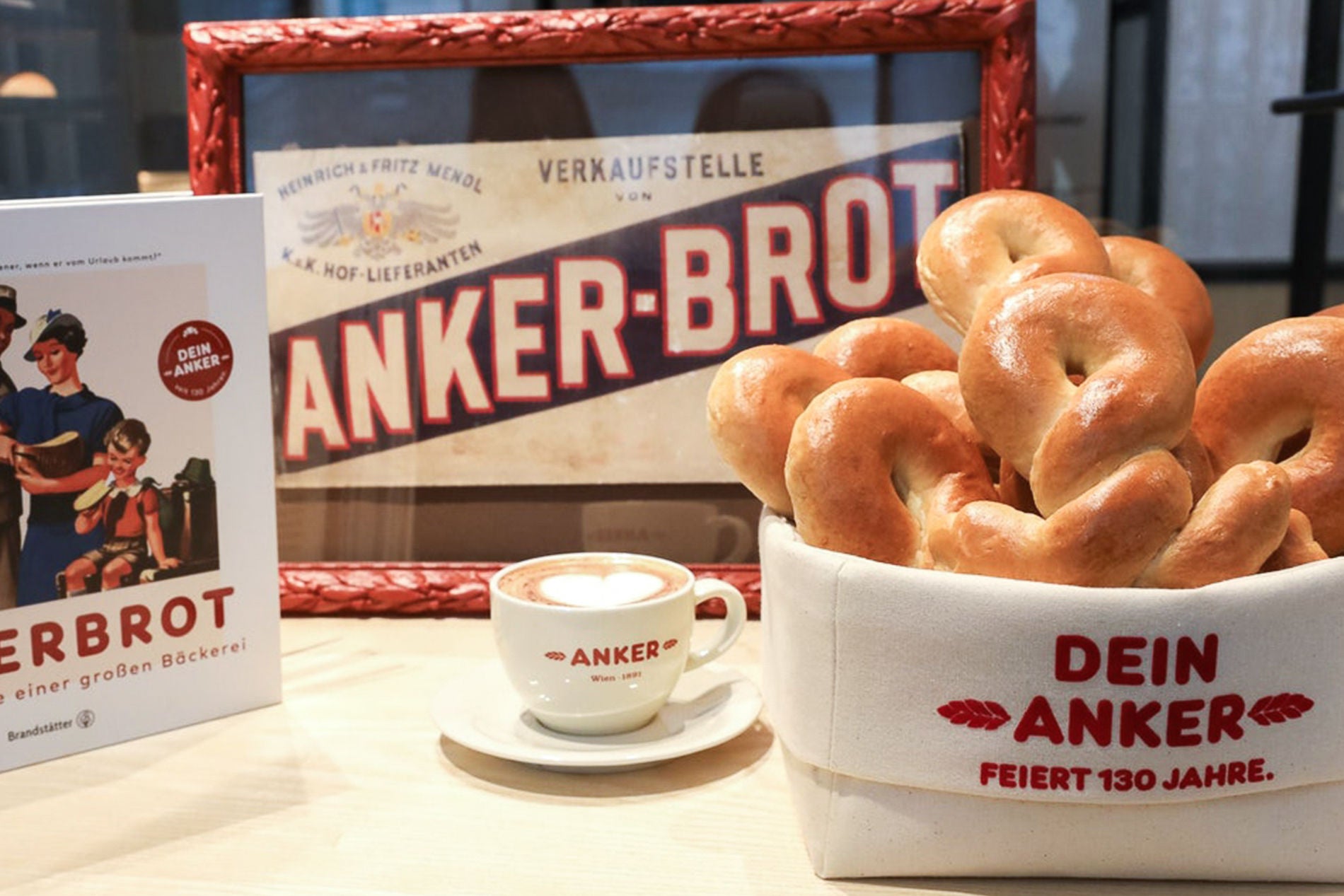
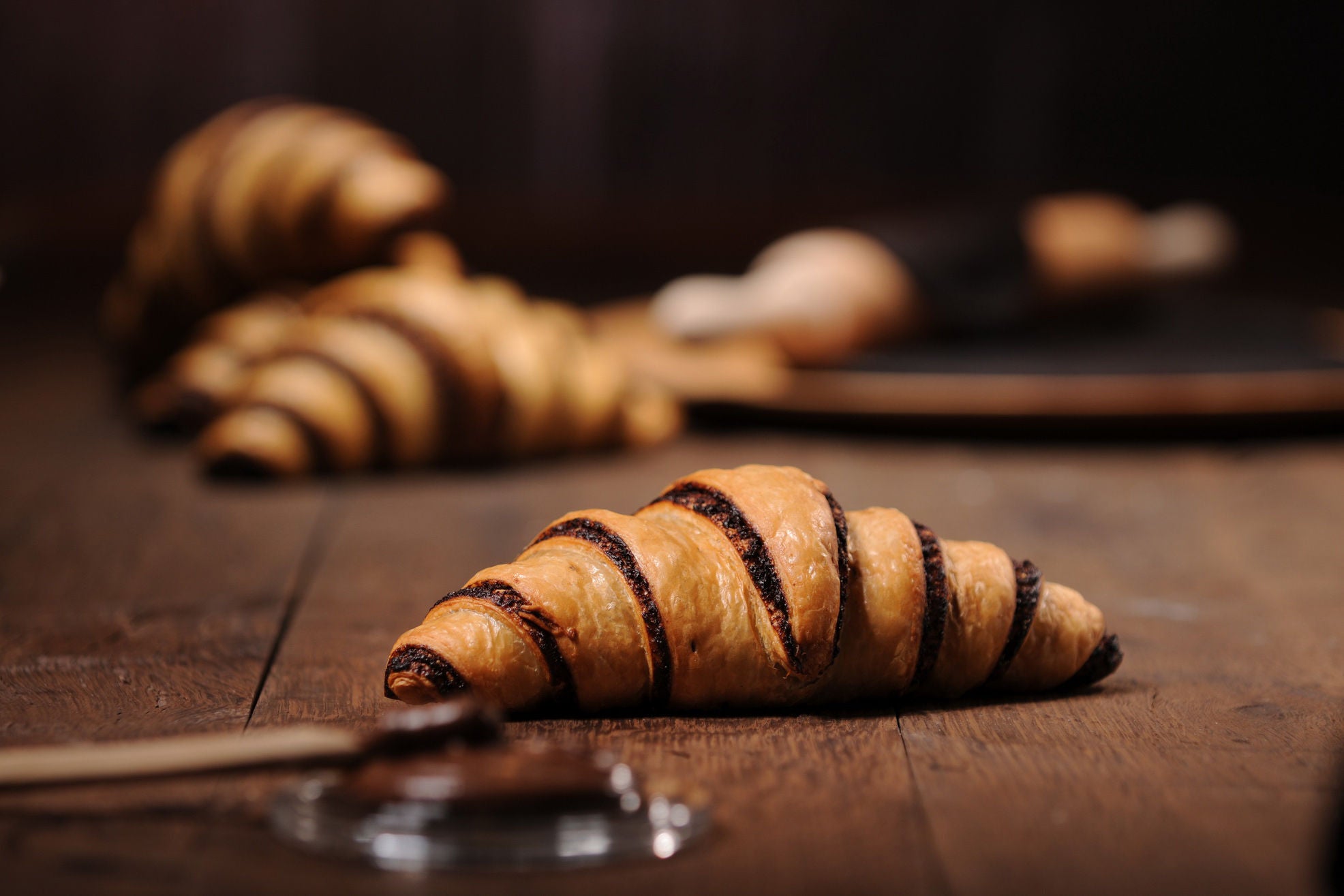
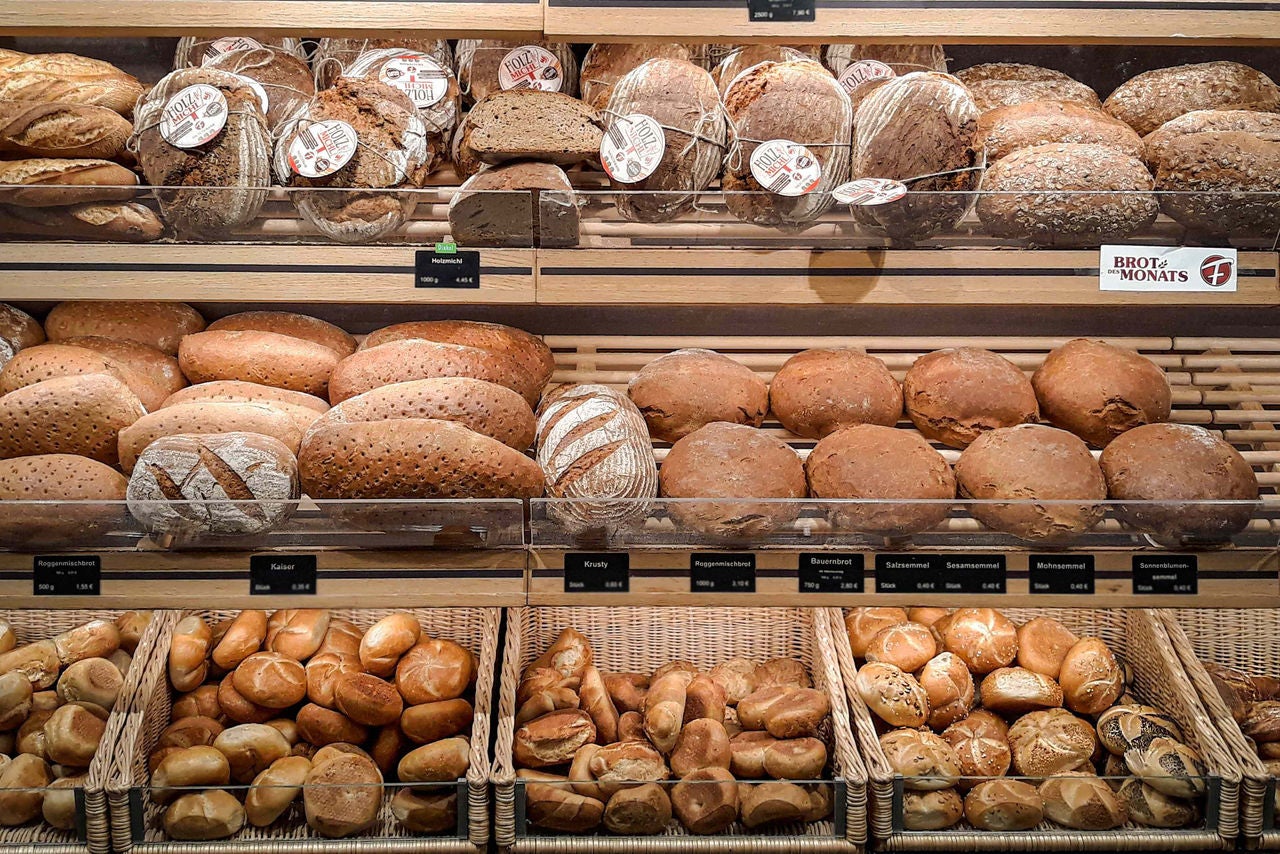
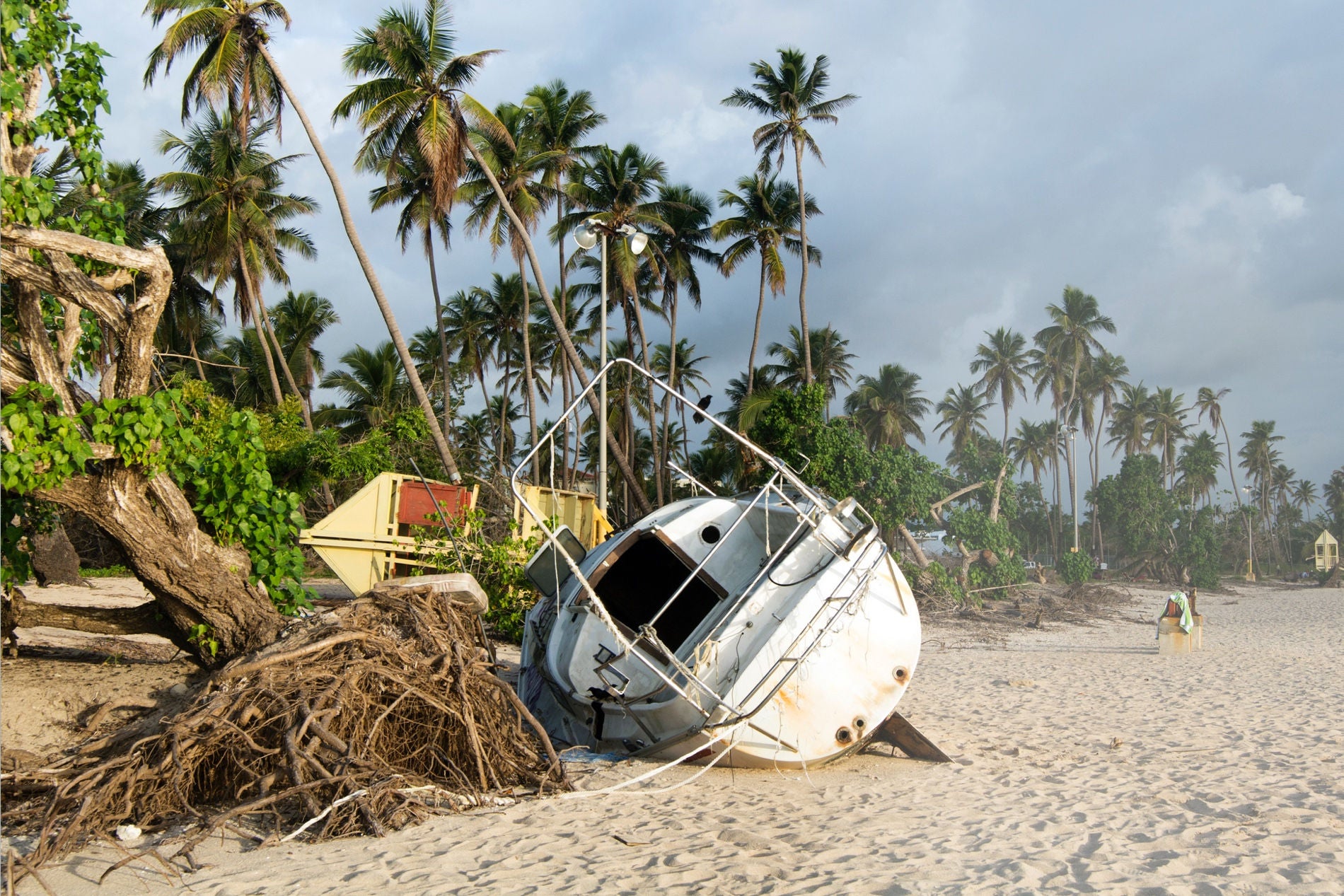